Discover What is Porosity in Welding and Its Impact on Structural Integrity
Wiki Article
The Science Behind Porosity: A Comprehensive Overview for Welders and Fabricators
Recognizing the complex mechanisms behind porosity in welding is crucial for welders and fabricators making every effort for flawless craftsmanship. As metalworkers explore the depths of this sensation, they uncover a world regulated by various elements that affect the formation of these tiny gaps within welds. From the composition of the base materials to the complexities of the welding process itself, a multitude of variables conspire to either exacerbate or relieve the existence of porosity. In this extensive guide, we will certainly untangle the scientific research behind porosity, exploring its effects on weld quality and introduction progressed methods for its control. Join us on this journey via the microcosm of welding blemishes, where precision meets understanding in the search of remarkable welds.Understanding Porosity in Welding
FIRST SENTENCE:
Exam of porosity in welding reveals critical insights right into the integrity and high quality of the weld joint. Porosity, identified by the existence of dental caries or gaps within the weld steel, is a common issue in welding processes. These spaces, if not effectively dealt with, can jeopardize the architectural integrity and mechanical properties of the weld, resulting in possible failings in the finished product.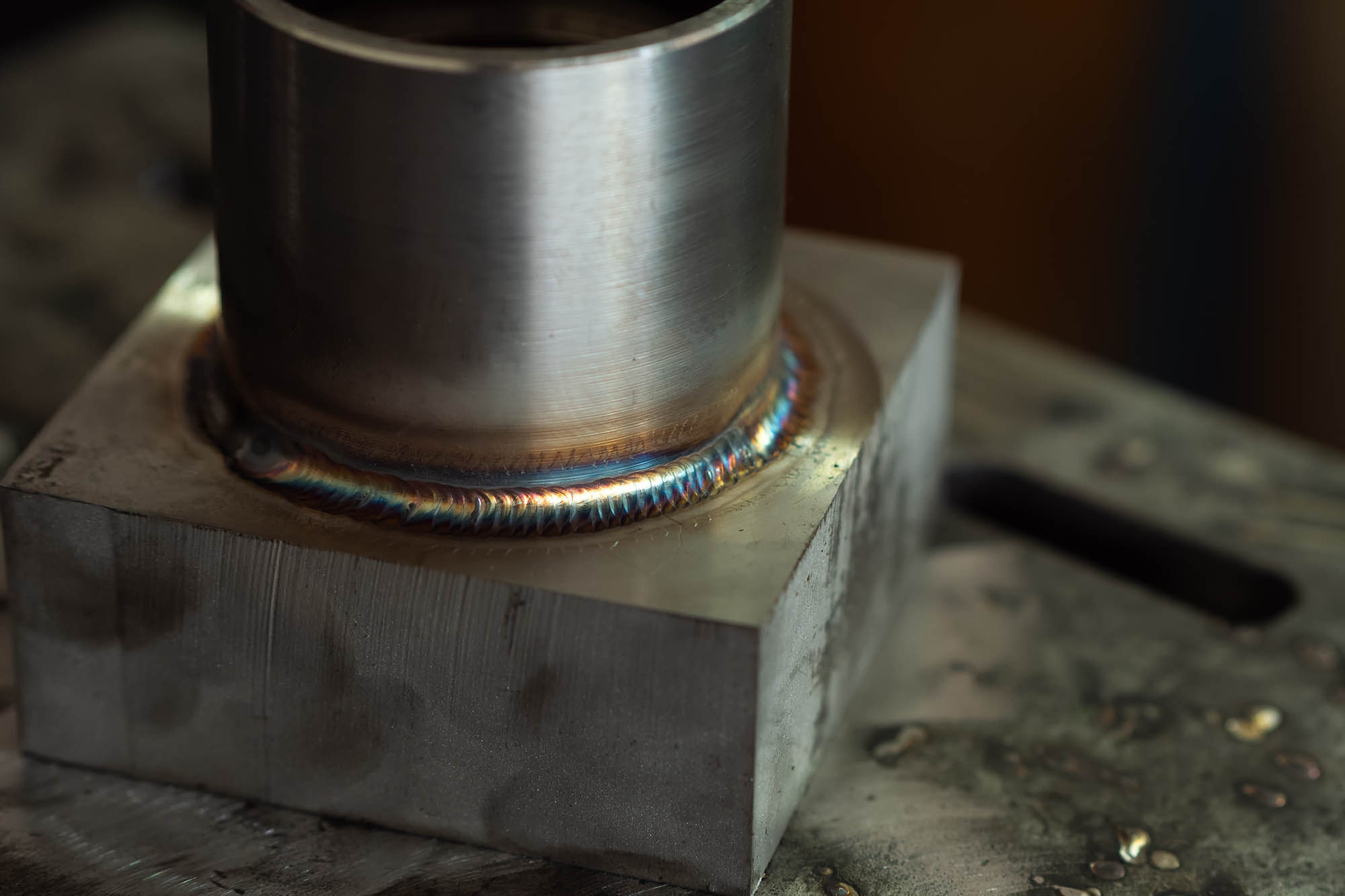
To find and evaluate porosity, non-destructive screening techniques such as ultrasonic testing or X-ray evaluation are frequently employed. These techniques permit the recognition of interior flaws without jeopardizing the integrity of the weld. By analyzing the size, form, and circulation of porosity within a weld, welders can make informed choices to improve their welding processes and attain sounder weld joints.
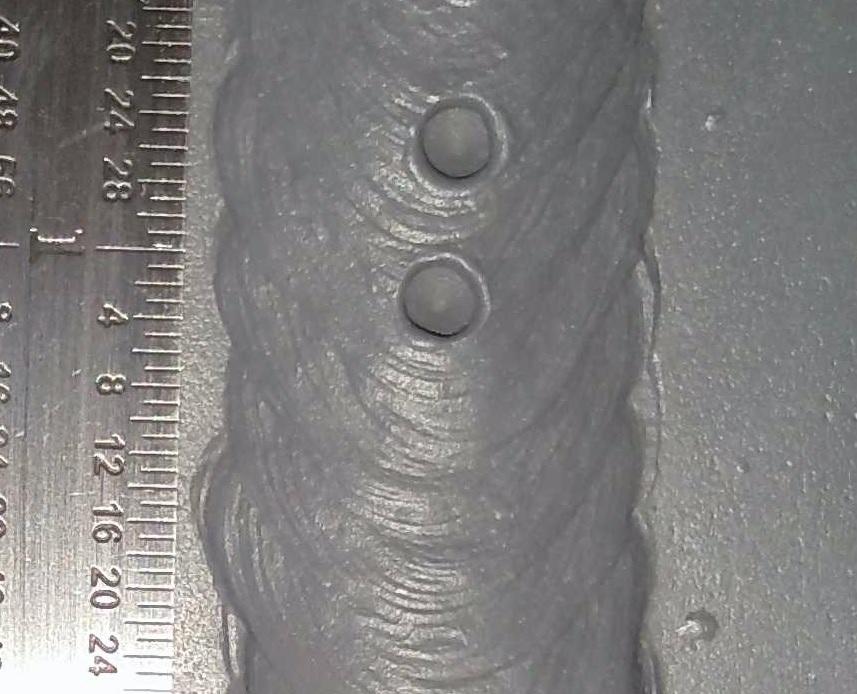
Variables Affecting Porosity Development
The occurrence of porosity in welding is influenced by a myriad of aspects, ranging from gas protecting effectiveness to the intricacies of welding criterion setups. One important factor adding to porosity development is inadequate gas securing. When the securing gas, normally argon or carbon dioxide, is not successfully covering the weld pool, climatic gases like oxygen and nitrogen can infect the liquified steel, causing porosity. Furthermore, the tidiness of the base materials plays a significant duty. Impurities such as corrosion, oil, or dampness can vaporize throughout welding, producing gas pockets within the weld. Welding parameters, consisting of voltage, present, travel rate, and electrode type, additionally impact porosity development. Using improper setups can create extreme spatter or warmth input, which subsequently can lead to porosity. The welding method used, such as gas metal arc welding (GMAW) or secured steel arc welding (SMAW), can affect porosity formation due to variants in warm circulation and gas protection. Understanding and managing these factors are necessary for minimizing porosity in welding procedures.Impacts of Porosity on Weld Quality
Porosity development significantly endangers the structural stability and mechanical homes of welded joints. When porosity exists in a weld, it develops spaces or tooth cavities within the material, minimizing the total strength of the joint. These gaps work as stress focus points, making the weld a lot more prone to splitting and failing under load. The existence of porosity likewise deteriorates the weld's resistance to rust, as the entraped air my website or gases within deep spaces can respond with the surrounding setting, causing degradation with time. Additionally, porosity can impede the weld's ability to withstand pressure or impact, further endangering the general quality and dependability of the welded structure. In essential applications such as aerospace, auto, or structural buildings, where security and resilience are critical, the destructive results of porosity on weld top quality can have severe consequences, stressing the value of lessening porosity with proper welding strategies and treatments.Strategies to Minimize Porosity
In addition, making use of the appropriate welding specifications, such as the proper voltage, current, and travel rate, is crucial in avoiding porosity. Maintaining a constant arc length and angle throughout welding additionally helps minimize the chance of porosity.
Making use of the ideal welding method, such as back-stepping or utilizing a weaving movement, can also help disperse warm equally and lower the chances of porosity formation. By implementing these methods, welders can properly minimize porosity and create premium bonded joints.
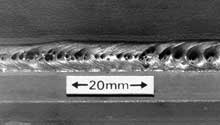
Advanced Solutions for Porosity Control
Applying innovative technologies and cutting-edge techniques plays a pivotal duty in accomplishing superior control over porosity in welding procedures. One innovative service is making use of innovative gas blends. Protecting gases like helium or a combination of argon and hydrogen can help in reducing porosity by giving better arc security and improved gas protection. Furthermore, employing sophisticated welding strategies such as pulsed MIG welding or modified environment welding can also assist reduce porosity concerns.Another sophisticated option entails making use of sophisticated welding devices. For example, making use of equipment with built-in features like waveform control anchor and sophisticated power resources can improve weld top quality and lower porosity risks. The implementation of automated welding systems with accurate control over parameters can significantly lessen porosity flaws.
Moreover, integrating sophisticated monitoring and evaluation technologies such as real-time X-ray imaging or automated ultrasonic testing can assist in discovering porosity early in the welding process, enabling immediate rehabilitative activities. Generally, integrating these advanced solutions can substantially boost porosity control and improve the overall quality of bonded elements.
Verdict
In conclusion, recognizing the science behind porosity in welding is you could try here crucial for welders and producers to generate premium welds - What is Porosity. Advanced solutions for porosity control can additionally boost the welding process and make sure a strong and reputable weld.Report this wiki page